UV curing technology uses specific wavelengths to trigger photoinitiators, enabling rapid curing of coatings, inks, or adhesives within seconds. Custom UV systems require precise optimization of curing area, irradiation intensity, and LED configuration to achieve energy-efficient, high-performance results across industrial, medical, and electronics applications.
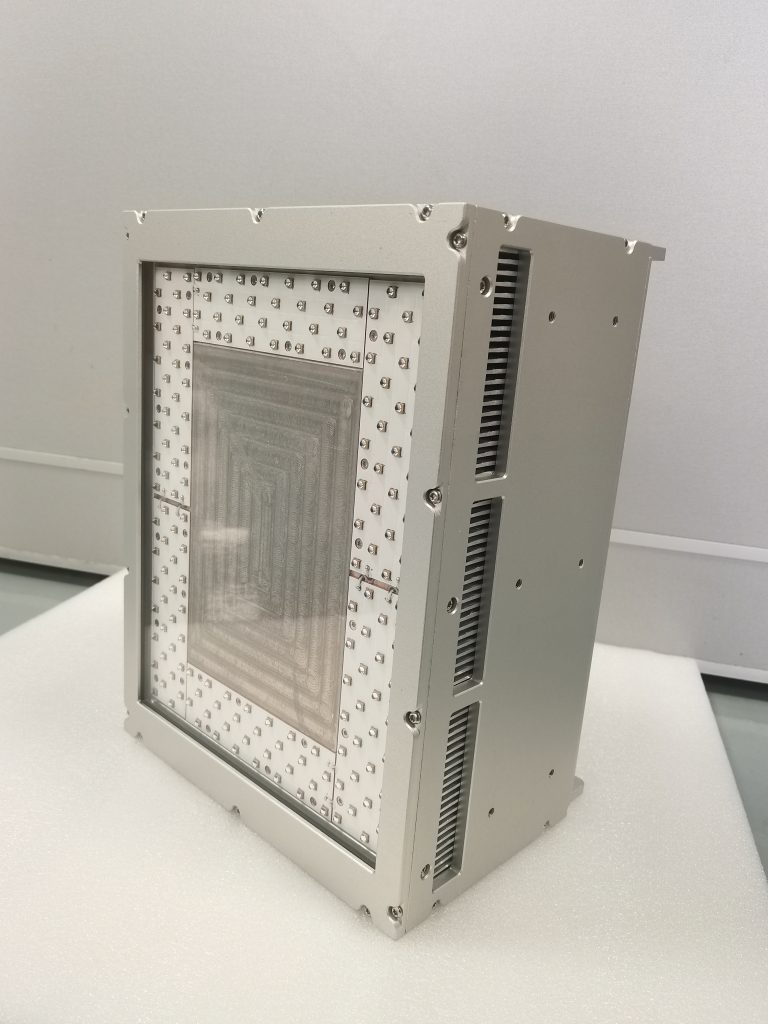
1. Curing Area: System Design & Layout
The curing area dictates UV source arrangement and equipment dimensions.
- Small Area (<0.1m²)
Applications: Microelectronics, medical device bonding.
Solution: Single high-power LED (≥5W/cm²) with collimating lens for 10-50mm spot diameter. - Medium Area (0.1-1m²)
Applications: PCB manufacturing, display lamination.
Solution: Linear/cellular arrays (6-12 LEDs) covering 300×200mm, edge uniformity >85%. - Large Area (>1m²)
Applications: Automotive coatings, roll-to-roll processing.
Solution: Modular LED arrays with conveyor synchronization and real-time intensity monitoring.
2. Irradiation Intensity: Material-Specific Energy Thresholds
Intensity (mW/cm² or W/cm²) determines curing speed and depth.
Material Type | Intensity Range | Curing Time |
---|---|---|
Low-viscosity adhesives | 50-100 mW/cm² | 3-10 sec |
High-density inks | 200-500 mW/cm² | 1-5 sec |
Thick resin coatings | 800-1500 mW/cm² | 0.5-2 sec |
Validation: Use radiometers to measure energy density (mJ/cm² = Intensity × Time) across the target surface.
3. LED Selection: Balancing Wavelength, Power & Thermal Management
UV-LEDs outperform mercury lamps with >20,000-hour lifespans but require tailored specs:
3.1 Wavelength Optimization
- 365nm: Deep penetration for dark/opaque materials (e.g., black inks).
- 395/405nm: Higher efficiency for clear coatings, safer for operators.
3.2 Power & Cooling
- Low-power (3-5W/chip): Ideal for heat-sensitive substrates.
- High-power (10-30W/chip): Requires active cooling (air/water) to maintain <80°C junction temperature.
3.3 Configuration Examples
- High-speed line: 395nm, 10×15W LEDs, 150W total, 1200mW/cm² @10cm.
- Precision optics: 365nm, 4×5W LEDs with 90% uniformity.
4. System Optimization Strategies
- Dynamic control: PWM dimming for conveyor speed adaptation.
- Safety: Shielding + IR filters to minimize ozone/thermal risks.
- Maintenance: Annual calibration to limit LED degradation (<5% intensity loss/year).
By aligning curing area, intensity profiles, and LED specifications, manufacturers can reduce cycle times by 30-50%. Partner with suppliers for prototype testing using UV energy integrators to validate performance before full-scale deployment.
Pro Tip: For niche applications (flexible substrates/high-temperature environments), provide material datasheets to refine spectral output and cooling requirements.